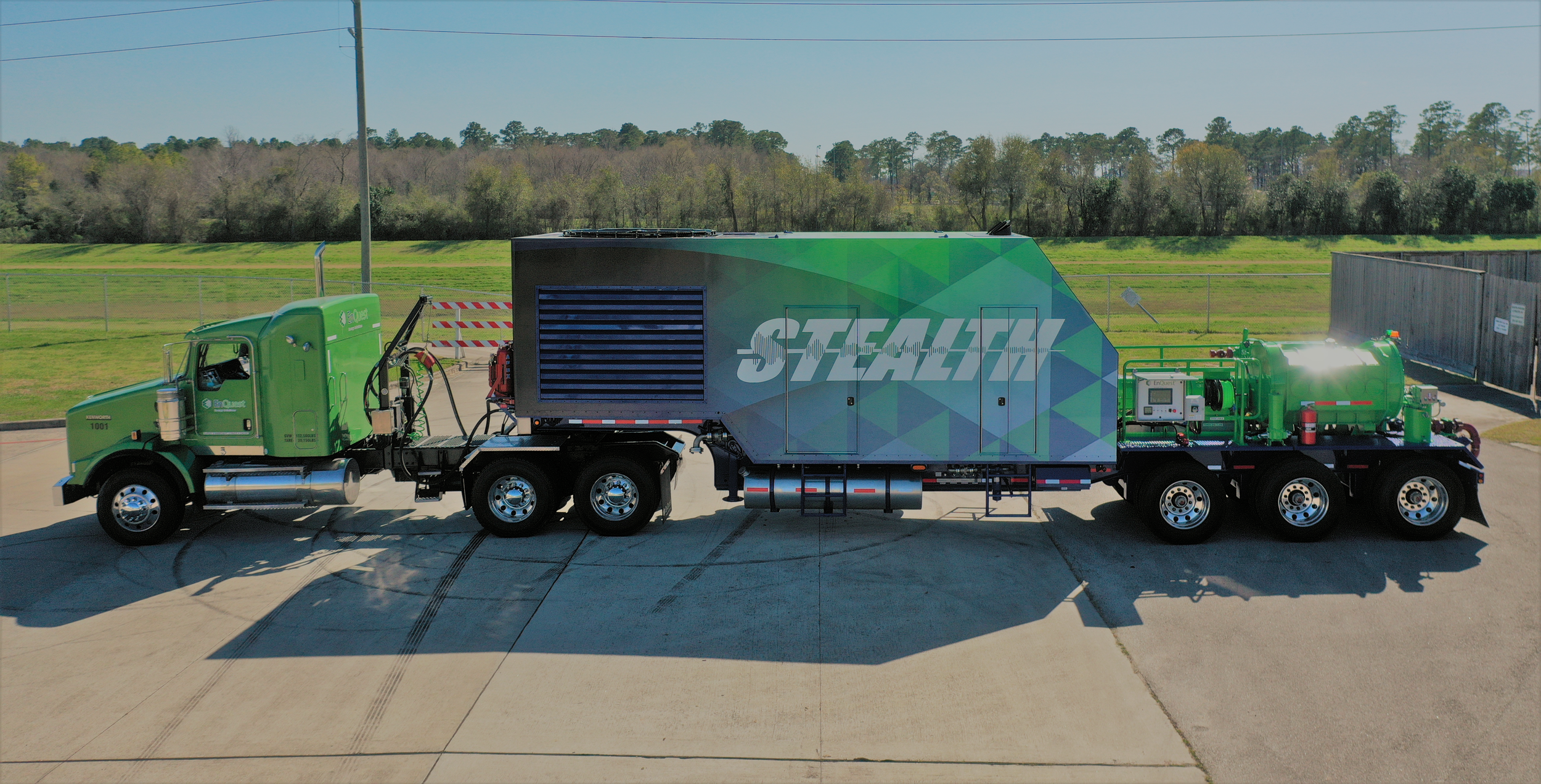
Case Study: The Stealth
Making fracturing safer through noise reduction technology
Project Highlights
months from design to fleet deployment
reduction in noise over conventional units
noise complaints
01. Problem
Fracturing is loud. To comply with local regulations and protect their workers, our customers needed a better approach.
02. Objective
Devise a comprehensive fracturing solution to protect personnel and satisfy any municipal noise ordinances.
03. Solution
The Stealth, a fully contained frac trailer with noise dampening technology for quiet blending and fracturing operations.
04. Result
Our StealthFrac and StealthBlender saw up to a 20dBA reduction in noise over conventional units, bringing the site well within compliance of municipal sound ordinances and removing the need for sound protection for workers.
Background
In recent years, the oil and gas industry has come to recognize that well operations are loud enough to qualify as a health hazard, not only for the people directly involved but for people who live and work nearby. Researchers have demonstrated that high-level noise is not the only culprit—constant low decibel sounds can disturb sleep and cause stress, which in turn can create a wide range of medical issues.
Hydraulic fracturing is no different in this regard to conventional drilling. Sound levels in excess of 100dBA have been reported during fracturing operations, well past the level at which hearing loss can occur.
Usually, fracturing workers opt for hearing protection in the form of earplugs or earmuffs to help them withstand the noise.
However, this causes its own hazards. Non-selective noise dampening may block vital auditory safety signals, such as the sound of a truck backing up at night, when many fracturing crews work. It also makes spoken communication difficult, often causing workers to remove their hearing protection to hear the conversation and thus exposing themselves to hearing damage.
EnQuest’s Answer
We set out to design a fracturing unit that would be not only state-of-the-art, but quiet enough to not have to require hearing protection during operations.
So we designed and patented an enclosure with custom sound-dampening technology to complement the 2500HP CAT Tier IV DGB dual fuel engine.
In fabrication, we incorporated new, patented construction techniques and material combinations of fiberglass, aluminum and sound dampening materials that would optimize sound blocking without being overly heavy.
We also made the enclosure removeable so it can be lifted off the unit for maintenance, if needed, as well as added access doors.
The cooling system is a major source of noise, so we worked with a trusted partner to utilize the quietest cooling system in the industry.
And because we wanted to prioritize safety in all forms, we installed AFEX dual agent fire suppression system and a gas detection system to detect natural gas leaks from the dual fuel system.
Ready to Roll
Within six months, the EnQuest team had designed, built, tested, and deployed an entire fleet of Stealth trucks. After extensive sound testing by a third party had verified the noise reduction Stealth units achieve, we proved its prowess in the field.